Paryleen coating systeem
Wat is Paryleen
Chemisch
PARYLEEN is de GENERISCHE BENAMING voor een serie van polymeren gebaseerd op p-Xylyleen
POLY (PARA-XYLYLEEN)
Algemene chemische Structuur
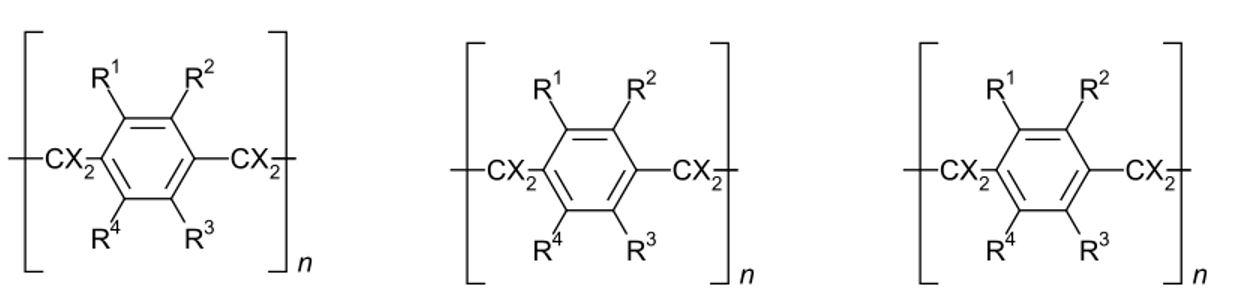
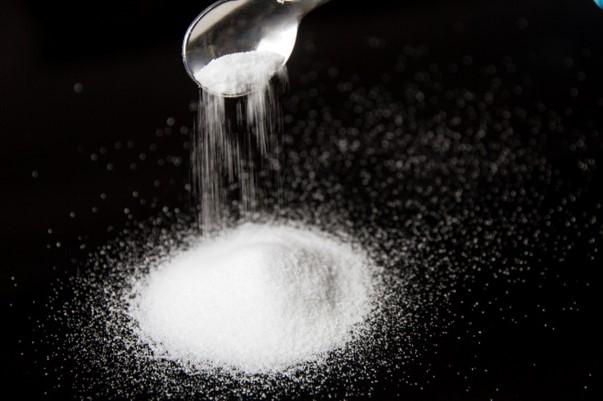
Substantieel
Grondstof van paryleen is beschikbaar in de vorm van een poeder
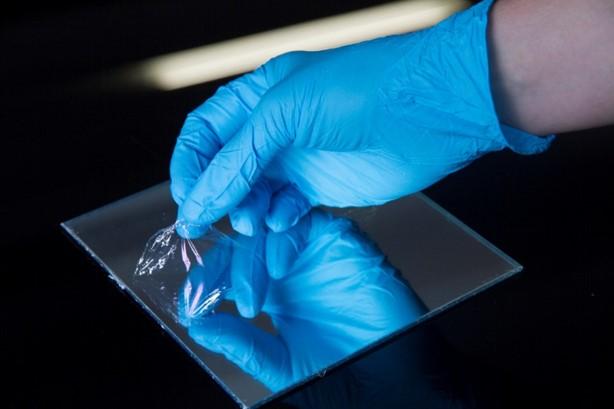
Na een chemisch opdampproces vormt parylene een polymeerfilm met buitengewone eigenschappen.
Aanzienlijke voordelen van de parylene-technologie
- Parylene vormt een zeer hoge en vooral betrouwbare bescherming tegen chemicaliën, omgevingsinvloeden en veroudering
- Vrij van bijproducten
- Perfect conforme coatings – Uniformiteit & perfecte dekkingsgraad
- Biostabiliteit, biocompatibiliteit, sterilisatievermogen en bioaanvaardbaarheid
- Lage applicatietemperaturen (kamertemperatuur)
- Goede droge smering
- Optisch transparant
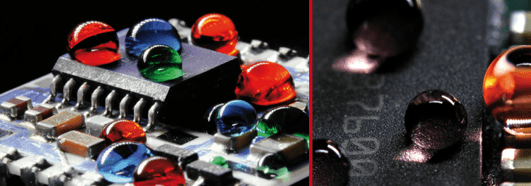
Toepassingen van paryleen
Elektronica / sensortechnologie
- Op plaatsen waar elektronische componenten worden blootgesteld aan corrosieve media, vocht of hoge straling
- Voor elektronica van hoogwaardige apparaten met een hoge veiligheidswaarde
- Voor significante levensduurverlenging van LED's, sensoren,..
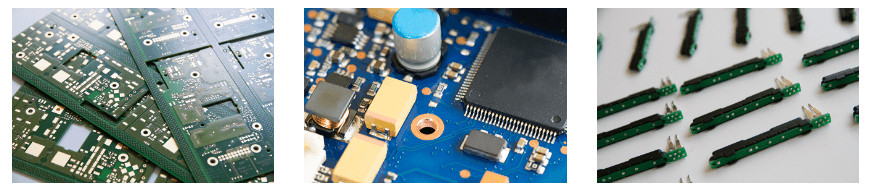

medisch / farmaceutisch
- Parylene is bestand tegen alle lichaamsvloeistoffen
- Minimale slijtage (beter dan PTFE) en zeer goede glij-eigenschappen maken het eenvoudig inbrengen van stents, naalden en katheters mogelijk
- Amerikaanse FDA-certificering voor direct contact met voedsel
- Gecertificeerd volgens ISO 10993 - Biologische eigenschappen en biocompatibiliteit van medische hulpmiddelen
- Parylene is bestand tegen alle gangbare sterilisatieprocessen
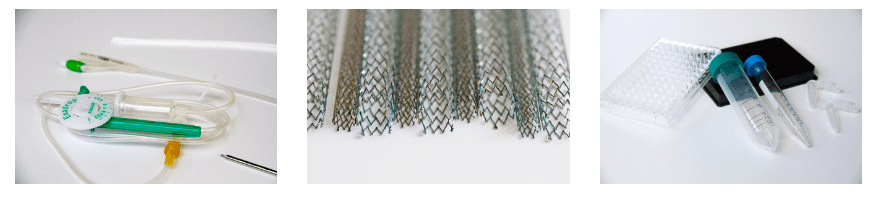
Luchtvaart / ruimtevaart
- Volgens systeemstoringen lopen zeer hoge waarden en mensenlevens het risico verloren te gaan. Daarom is de inspanning voor de best mogelijke bescherming van de vitale componenten in elk geval de moeite waard.
- Certificering volgens de hoogste lucht- en ruimtevaart- en militaire normen (US MIL-I-46058C, UL-genoteerd, NBC AR 70 / AFR 80-38 / Navinst 3400.2) biedt veiligheid, zelfs op andere gebieden met hoge stress en veiligheidsrelevantie.
- Bescherming tegen hoogenergetische straling met Parylene HT bij lage laagdikte (eisen van een lage gewicht/volume-verhouding).
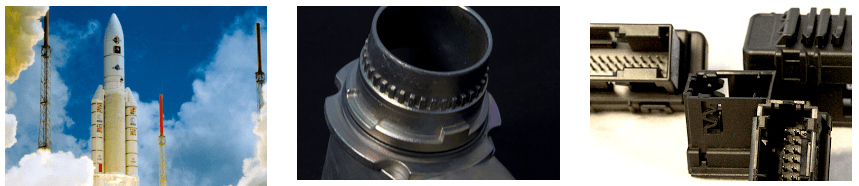
Luchtvaart / ruimtevaart
- Coating van pakkingen (O-ringen) voor eenvoudigere montage (lage wrijvingscoëfficiënt), of om de levensduur te verlengen.
- Beschermende en zelfreinigende (hydrofobe) coating van optische componenten.
- Elastomeren zijn vaak gevoelig voor ozon, koolwaterstoffen, UV. Parylene biedt een langdurige bescherming.
- Barrièrecoating op containers, flacons of buizen.
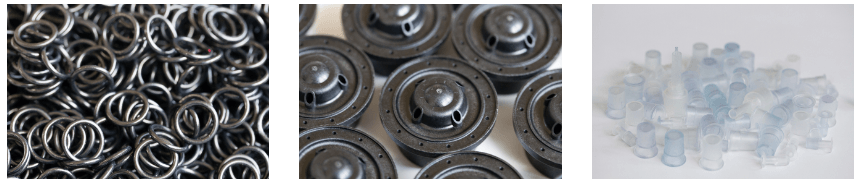
Vervaardiging van paryleencoatings door chemische dampafzetting
Dimer →→
Monomer →→
Polymer
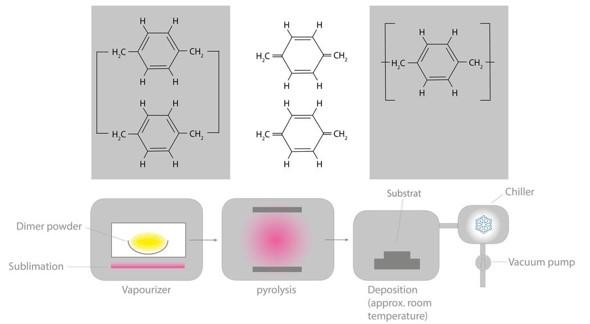
Kamertemperatuur
Parylene-coating kan op bijna alle materialen en multimateriaal-assemblages worden uitgevoerd
De enige beperkingen zijn:
- Vacuümvermogen
- De dampdruk van elk materiaal of elke verbinding waaruit het onderdeel bestaat, moet voldoende laag zijn om verdamping of sublimatie bij kamertemperatuur (max. 40°C) tijdens het vacuümproces te voorkomen.
Onderdeel maat
- Afmetingen worden beperkt door het volume van de depositiekamer
- Kamergrootte P300: Hoogte: 720 mm Ø: 700 mm
- Opmerking: zeer grote kamer kan worden gerealiseerd
Oppervlakken reinheid
De aanwezigheid van zelfs kleine hoeveelheden oppervlakteverontreinigingen, olie, vet, oxiden enz. kan de hechting van de coating aan het substraat fysiek aantasten en verminderen
Adhesieprestaties zijn een combinatie van:
Mechanische hechting:
Ruwheid – Porositeit Complexe geometrie
+
Dekkingsgraad van paryleen
Chemische hechting:
Om de chemische hechting te verbeteren, kunnen specifieke hechtingspromotor(en) worden gebruikt
+
Monomeer reactiviteit
→ → Oppervlaktevoorbehandeling is een sleutelfactor die het uiteindelijke succes van een paryleenbehandeling beïnvloedt.
Dekkingsmethodes
Standaardproces:
Onderdelen zijn gerangschikt op carrousel, die tijdens het proces langzaam in de kamer zal draaien. Uitgelegd op trays of opgehangen aan ondersteuningsapparaat
Voor brosse onderdelen en apparaten Contactpunten niet gecoat. (bij maskering: contactpunten komen overeen met gemaskeerde gebieden).
Tuimelingsproces:
Onderdelen worden in bulk gecoat in een gesloten vat dat langzaam draait, waardoor onderdelen die samengaan met coating worden vermeden.
Voor vrij kleine onderdelen en grote hoeveelheden
- volledige inkapseling
- “Laag schadelijk materiaal” zoals ferrieten, elastomere delen, … Hameren, verlies van transparantie: coating min of meer melkachtig.
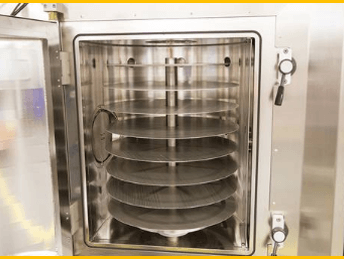
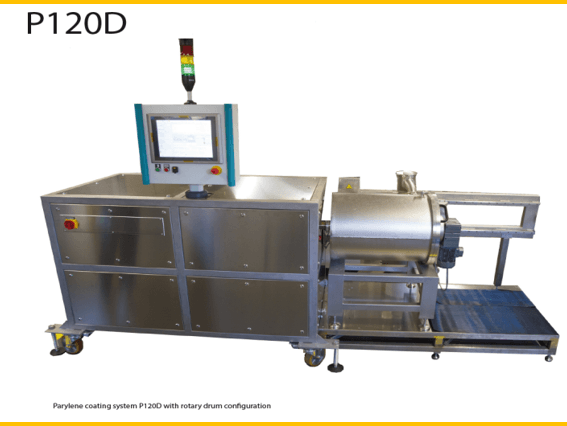
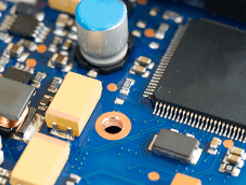
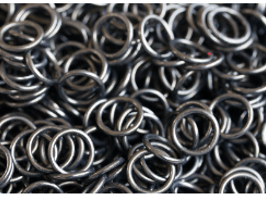
De belangrijkste verschillende soorten parylenen en hun specifieke kenmerken

Parylene N
Basismodel, alleen opgebouwd uit de atomen waterstof en koolstof. Maar niet het meest voorkomende type. Buitengewoon goede penetratie in spleten en gaten. Optimale diëlektrische eigenschappen en diëlektrische sterkte en daarom de voorkeur voor het coaten van elektronische componenten en samenstellingen. Laagste wrijvingscoëfficiënt, populair bij het aanbrengen van katheters. FDA-conform
Parylene C
Het meest gebruikte product met uitstekende barrière-eigenschappen. Hoge vochtbescherming en ondersteund door de goede hydrofobe eigenschappen. Hoge elasticiteit, daarom geschikte coating voor kunststoffen en rubbers. Lage wrijvingscoëfficiënt. Hoge depositiesnelheid (tot 10 micron/h). FDA-conform
Parylene D
Lange tijd gebruikt vanwege de verhoogde temperatuurstabiliteit. Maar het is ook erg hydrofoob. Gebruikt voor het beschermen van elektronische componenten in de lucht- en ruimtevaartindustrie.
Parylène F-VT4
Omdat het thermisch nog hogere belastingen weerstaat dan Parylene D, verdringt het dit steeds meer in toepassingen met een hogere temperatuurbelasting. Het is veel goedkoper dan Parylene HT.
Parylene F-AF4
Veruit de hoogste temperatuurstabiliteit van alle Parylene-types. Bovendien is dit type zeer ongevoelig voor agressieve stralingsblootstelling, vooral voor UV. De duurste uitvoering, daarom alleen gebruikt wanneer deze speciale eigenschappen noodzakelijk zijn.
→ → Diener electronic ondersteunt u bij het vinden van het juiste paryleentype voor uw product
Voordelen van paryleen in vergelijking met andere coatings
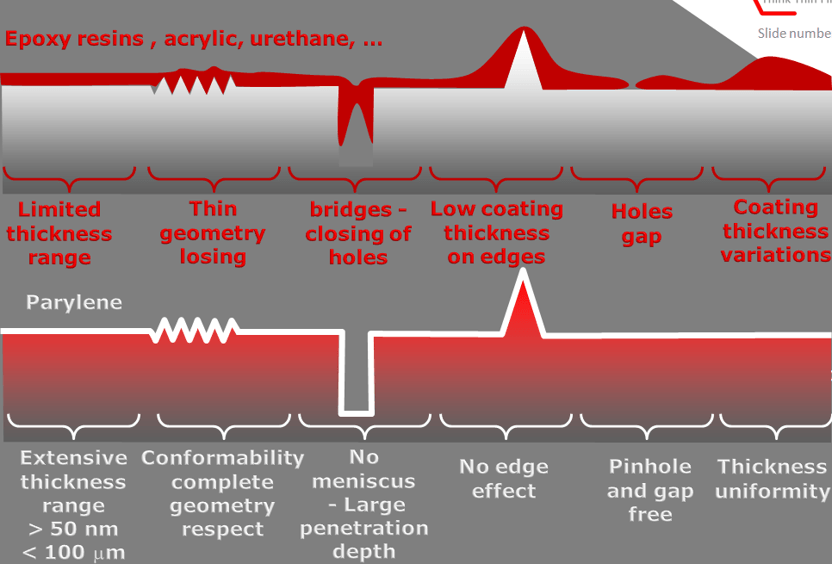